Greetings, future accounting stars! As you embark on the incredible journey towards your CA dreams, the intricacies of cost accounting become your essential companions. Today, we zoom in on prime cost, a cornerstone concept for mastering production efficiency and profitability analysis. So, CA aspirants, prepare to dive into the exciting world of prime cost!
Demystifying the Core:
Imagine prime cost as the sturdy foundation of a building. It encompasses the direct costs directly linked to producing a single unit of your product. Think of it as the raw materials you transform and the labor that breathes life into them. Unlike its counterparts, the prime cost stays clear of overheads and indirect expenses, keeping the focus solely on the essentials.
The Pillars of Prime Cost:
- Direct Materials: The tangible components that make up your masterpiece, like the wood that sings in your handcrafted furniture or the fabric that dances on your designer dress.
- Direct Labor: The wages paid to the heroes behind the scenes, the bakers meticulously crafting your morning brioche or the tailors stitching dreams into reality.
Formula:
Prime Cost = Cost of Direct Materials + Direct Labor Cost
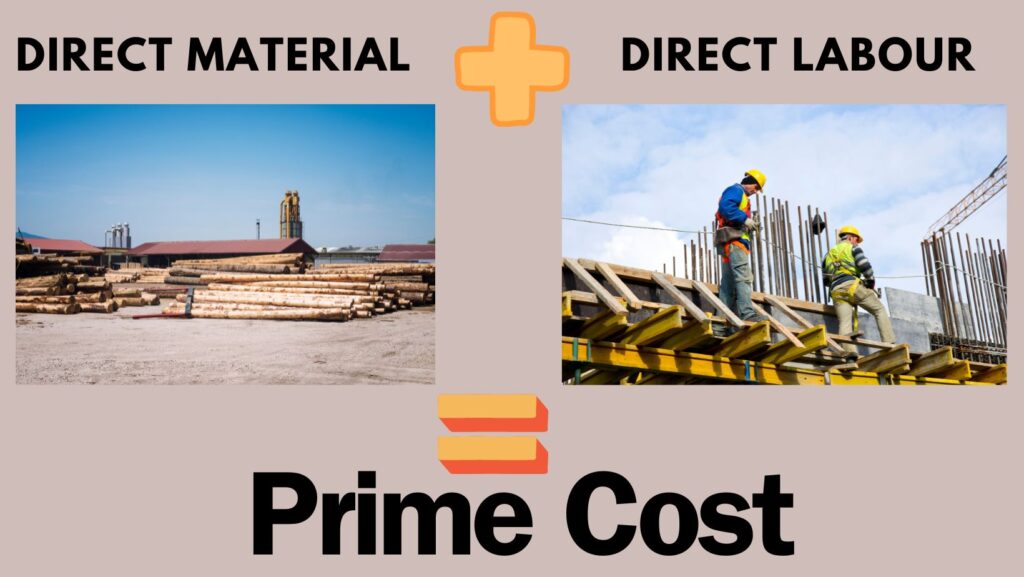
Image Credit Goes to www.canva.com
Why Does Prime Cost Matter?
Understanding prime cost unlocks a treasure trove of insights for businesses and aspiring CAs alike:
- Cost Control Champions: Knowing your prime cost empowers you to become a cost-control ninja, identifying and managing expenses effectively.
- Pricing Powerhouse: Prime cost forms the base for cost-plus pricing, allowing you to calculate product selling prices that ensure healthy profit margins.
- Efficiency Evangelist: By analyzing trends in prime cost over time, you can become an efficiency guru, pinpointing areas for production optimization and cost reduction.
- Profitability Pathfinder: Prime cost plays a pivotal role in calculating contribution margin, which reveals a product’s ability to cover fixed costs and contribute to overall profitability.
Beyond the Textbook: Fun Facts about Prime Cost!
- Prime Cost Olympics: Did you know there are industries where prime cost dominates? Think bakery delights, where flour, sugar, and eggs take center stage, or furniture factories where wood whispers its price.
- Hidden Prime Cost Culprits: Beware of waste (both material and labor)! It can inflate your prime cost without adding value, making you a prime suspect in the efficiency case.
- Prime Cost Predictions: Mastering prime cost analysis empowers you to predict the impact of raw material price fluctuations or labor cost changes, making you a business fortune teller (minus the crystal ball).
Examples that Bring it Home:
Example 1: The Flourishing Bakery
Imagine a bakery producing delectable cakes. The cost of flour, sugar, and eggs are the direct materials, while the wages of bakers transforming them into sweet masterpieces are the direct labor costs. By calculating the prime cost per cake, the bakery can:
- Be a flour price fluctuation forecaster, adjusting costs and pricing accordingly.
- Analyze baking processes to identify potential time and ingredient-saving techniques.
- Set cake prices that ensure a sweet profit even after covering rent, electricity, and other indirect costs.
Example 2: The Furniture Symphony
Picture a furniture factory where wood, fabric, and metal sing in harmony. The cost of these materials forms the direct materials, while the wages of carpenters, upholsterers, and assemblers crafting furniture pieces are the direct labor costs. Knowing the prime cost per furniture item allows the factory to:
- Compare the cost-effectiveness of different wood types and upholstery materials, making informed purchasing decisions.
- Evaluate the productivity of individual workers, identifying areas for training and skill development.
- Negotiate competitive prices with suppliers based on a clear understanding of raw material costs.
Example 3: The Garment Gala
Imagine a garment manufacturer where fabric, thread, and buttons weave magic. The cost of these materials forms the direct materials, while the wages of tailors, sewers, and quality inspectors bringing garments to life are the direct labor costs. By tracking the prime cost per garment, the manufacturer can:
- Analyze the impact of different fabric qualities on production costs, choosing value without compromising style.
- Assess the efficiency of cutting and sewing processes to minimize fabric wastage, becoming a sustainability champion.
- Optimize labor costs by implementing lean manufacturing practices, ensuring smooth production flow.
Key Takeaways for CA Aspirants:
- Ace the formula for prime cost calculation, making it your secret weapon.
- Recognize the distinction between prime cost and total cost of production, becoming a cost accounting master.
- Understand the significance of prime cost in cost control, pricing decisions, and profitability analysis, making informed business decisions.
- Apply your knowledge of prime cost to real-world business scenarios like the captivating examples provided, showcasing your practical understanding.
Frequently Asked Questions (FAQs) Continued:
Q: Does the prime cost include overheads like factory rent and electricity?
A: No, remember, prime cost only considers direct costs directly attributable to production. So, rent, electricity, and other overheads are accounted for separately as indirect costs.
Q: How does prime cost differ from conversion cost?
A: Prime cost serves as the foundation, laying the groundwork with direct materials. Conversion cost builds upon this foundation, adding direct labor to the equation. In simpler terms, conversion cost reflects the total cost of transforming raw materials into finished goods, including the labor involved.
Q: Is prime cost analysis relevant for service businesses?
A: While the concept of prime cost primarily applies to manufacturing, service businesses can adopt similar principles. They can identify and analyze direct costs like employee salaries and materials used to deliver the service. For instance, a consulting firm might track the salaries of consultants directly involved in a project and the cost of materials like research reports used during the engagement.
Beyond the Basics: Limitations and Considerations
While prime cost offers valuable insights, it’s crucial to understand its limitations:
- Blind to Indirect Costs: Prime cost doesn’t consider overheads and other indirect expenses like rent, utilities, and administrative costs. These expenses still impact production, so relying solely on prime costs might provide an incomplete picture of total production costs.
- Industry Dependence: Its relevance varies across industries. In labor-intensive industries like garment manufacturing, direct labor might dominate prime cost. However, in capital-intensive industries like steel production, the cost of raw materials might play a more significant role.
- Potential Misinterpretation: If overheads are high compared to direct costs, relying solely on prime cost for pricing or efficiency analysis can lead to misinterpretations. Always consider the total cost of production for comprehensive decision-making.
Mastering Prime Cost: Additional Tips and Tricks
- Embrace Technology: Utilize accounting software to efficiently track and analyze direct materials and labor costs, saving you time and effort.
- Benchmarking: Compare your prime cost with industry benchmarks to identify areas for improvement and stay competitive.
- Continuous Improvement: Regularly review and refine your prime cost calculations to ensure accuracy and reflect evolving production processes.
Remember, CA aspirants, the prime cost is a stepping stone. Use it as a foundation to build a deeper understanding of cost accounting and unlock your potential to optimize production, make informed pricing decisions, and contribute to business profitability.
Bonus Section: Dive Deeper into Prime Costing Methods
For those seeking to explore further, here’s a glimpse into different prime costing methods:
- Normal Costing: Uses average costs for materials and labor, suitable for stable production environments.
- Standard Costing: Predefined expected costs for materials and labor, ideal for identifying variances and controlling costs.
- Actual Costing: Uses actual costs incurred, suitable for projects with unique requirements or fluctuating costs.
Choose the method that best aligns with your business needs and accounting practices.
Conclusion:
By demystifying prime cost and its intricacies, you’ve taken a significant step towards mastering cost accounting. Remember, the journey doesn’t end here. Continue exploring, apply your knowledge in real-world scenarios, and watch your understanding blossom. As you conquer the CA exams, carry the torch of prime cost analysis, illuminating the path towards production efficiency and business success.
Do Check Out our Articles on various Accounting issues by clicking here.
Pingback: Conquer the Process Costing Maze: Normal vs. Abnormal Loss & Ace your Exams!